TM 55-1520-240-23-9
11-181
INSTALL PITCH OR ROLL INTERMEDIATE BELLCRANKS
(Continued)
11-181
Make sure bushings are in bellcranks
and link before installing bolts or
component damage will result.
NOTE
Impedance bolts are installed in flight
control connections. These bolts are
self-retaining and require a special
nut and torque (Task 1-13).
Procedure is same to install pitch or
roll intermediate bellcranks except
where noted. Roll bellcrank is shown
here.
1.
Remove nut (1), two washers (2 and 3), and bolt
(4) from support (5). Slide bolt through hole (6).
FLIGHT SAFETY PARTS
This is an installation critical flight
safety part. All aspects of its assembly
and installation must be ensured at
each joint connection and mounting to
the airframe.
Ensure that all bushings are properly
installed (including orientation) in
each input and output clevis of the
idler assembly.
Ensure idler hub bearings are
serviceable and properly installed.
Ensure proper attaching hardware
(impedance type bolt, nut, and
washers) is installed including
verification of bolt head orientation,
torque, and installation of cotter pins.
Loose attachments within flight control
primary linkage will degrade aircraft
control. Missing components will
cause loss of control.
2.
Position roll intermediate bellcrank (7), lug (8)
inboard and forward on support (5). Install bolt
(4), two washers (3 and 2) and nut (1). If pitch
intermediate bellcrank is being installed, install
bolt with head inboard.
3.
Torque nut (1) to 30 to 45 inch-pounds. Install
cotter pin (9). If pitch bellcrank is being installed,
torque nut to 60 to 90 inch-pounds.
4.
Remove nut (10), two washers (11 and 12) and
bolt (13) from link (14).
5.
Install bolt (13), two washers (12 and 11) and nut
(10). Do not tighten at this time.
6.
Remove nut (15), two washers (16 and 17). and
bolt (18) from link (19).
7.
Position link (19) on bellcrank (7). Install bolt
(18), two washers (17 and 16) and nut (15).
8.
Torque two nuts (10 and 15) to 30 to 45
inch-pounds. Install two cotter pins (20 and 21).
9.
Check three bolts (4, 13, and 18). Bolts shall not
rotate with torque less than 10 inch-pounds.
There shall be no axial looseness. If bolt rotates
or is loose, add washer under nut, and repeat
step 3 or 8.
INSPECT
11-718
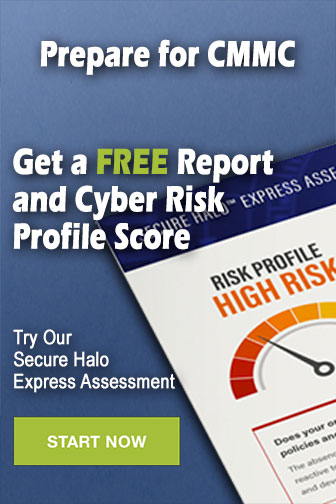