TM 55-1520-240-23-6
7-1
FLIGHT CONTROL HYDRAULIC SYSTEM
(Continued)
7-1
THEORY OF OPERATION
Both flight control hydraulic systems work in the same
manner. Hydraulic fluid pressurized to 3,000 psi leaves
the power source (transmission-driven pump, PTU
pump, or ground power unit) and enters the power
control module. In the module, it passes through a
monitored filter, pressurizes an accumulator, and flows
through a pressure-operated valve out of the module.
NO BREAK - WORK HARDER
From the module, the fluid flows to pressurize the
pivoting and swiveling servocylinders at each rotor head.
It then enters the lower controls system module in the
flight controls closet area.
NO BREAK - WORK HARDER
The lower controls module contains a pressure reducer
that drops line pressure from 3,000 to 1,500 psi. A
return line carries excess fluid back to the power control
module. Fluid exits the module at 1,500 psi through
two ports. An upper port leads to the ILCA manifold
to provide boost for the lower controls. The lower port
leads to the AFCS extensible link port in the manifold.
NO BREAK - WORK HARDER
Pressurized fluid from both hydraulic systems enters a
two-piece ILCA manifold. Four ILCAs are mounted on
the manifold. The two that boost pitch and roll control
inputs are on one side. Those that boost yaw and thrust
inputs are on the other side.
NO BREAK - WORK HARDER
The upper half of each manifold supplies fluid to all
ILCAs from the No. 1 system. The lower half supplies
fluid from the No. 2 system. Because the thrust ILCA
does not have an extensible link, fluid from the lower
port of the lower controls module is not directed to that
actuator.
NO BREAK - WORK HARDER
Like the manifold, each ILCA is split into two halves. The
top half is pressurized by the No. 1 hydraulic system,
the bottom half by the No. 2 system. Check valves in the
manifold prevent fluid loss when an ILCA is removed.
NO BREAK - WORK HARDER
When AFCS is switched off, a solenoid valve in each
lower controls module closes off fluid flow to the
extensible link controls in the ILCA. In this mode, all four
ILCAs act in the same manner. Pilot input displaces a
control valve in the ILCA, routing hydraulic fluid to an
internal actuator piston. The piston extends or retracts
and the motion is transferred to the upper controls.
NO BREAK - WORK HARDER
When AFCS is switched on, the solenoid valve in the
lower controls module opens and pressurized fluid
activates the extensible link on each of the three ILCAs
so equipped. Servo valves on the ILCA respond to
input from the AFCS computers to move the link. The
motion is transferred directly to the output link of the
ILCA moving the upper controls independently of input
link motion.
NO BREAK - WORK HARDER
Low pressure return fluid leaving each ILCA is routed
through ports in the manifold and a return line to a return
port in the power control module. It passes through a
monitored return filter and out of the module.
NO BREAK - WORK HARDER
If the power source is the flight control pump or the
power transfer unit, fluid leaving the module is circulated
through the reservoir cooler before being discharged to
the power source. A thermal switch in the discharge
port of the reservoir cooler turns on a cooling fan when
fluid temperature reaches about 145ºF. When fluid
temperature drops to about 130ºF, the switch turns the
fan off.
NO BREAK - WORK HARDER
If the power source is an external ground power unit,
fluid leaving the module is discharged directly to the unit.
7-8
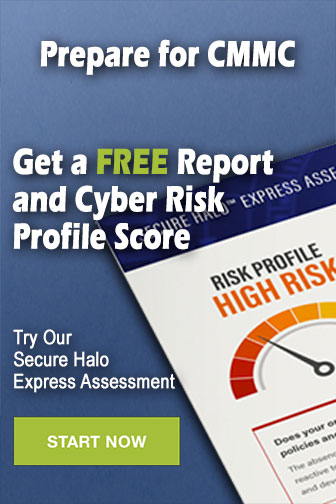