TM 55-1520-240-23-3
4-159
LEAK TEST FADEC P3 SIGNAL LINE
(Continued)
4-159
4.
If there is no significant drop in pressure after
one minute:
a.
Working on one connection joint at a time,
apply a liberal coating of soap solution to
each joint in the P3 system.
b.
Outside of the cabin, apply soap (E351) to
the P3 fitting and the coupling on the engine
shelf.
c.
In the cabin starting from the DECU fitting
and working aft, apply a liberal coating
of soap (E351) to each connection joint
including around the drain cartridge.
d.
If leaks are observed, mark them with a
grease pencil.
e.
De-pressurize the system, and repair the
leaks as required.
f.
Slowly pressurize the system to 100 psi and
inspect for leaks.
g.
Upon successful completion of the leak
check, go to step 6.
5.
If there is a significant drop in pressure:
a.
Reduce the pressure to 0 psi and inspect all
P3 connections and repair as necessary.
b.
Go to step 3.
6.
Close the valve (5) on the pressure source.
7.
At the drain cartridge, push up on the cartridge
condensate release mechanism to relieve the
pressure in the P3 system.
8.
Remove the air source hose (4) from the P3
hose (1).
Before reconnecting the P3 pressure
hose to the P3 tee filling on the
HMA, make sure that the 0.060 inch
orifice in the tee fitting is visible and
unobstructed. If not visible, the tee
fitting is installed backwards and must
be rotated. Remove any obstruction
from the orifice.
9.
Connect the P3 pressure hose (1) to the P3 tee
fitting (2).
INSPECT
FOLLOW-ON MAINTENANCE:
Install acoustic blankets as required.
Close engine access cover (Task 4-50).
Close engine work platform (Task 2-2).
Disassemble test setup.
END OF TASK
4-519/(4-520 blank)
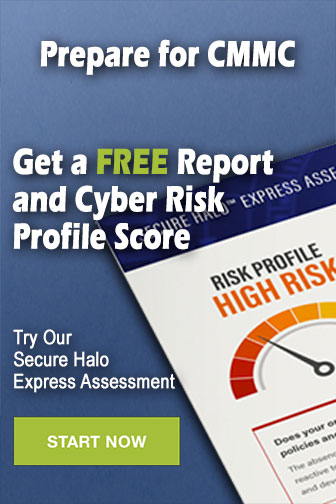